Celebrating Innovation: The CellSeal CryoCase One Year Later
Since its launch at the 2024 ISCT Annual Meeting, the CellSeal® CryoCase is poised to become a cornerstone solution for Cell and Gene Therapy (CGT) and biopharmaceutical storage. Designing this ideal cryostorage container involved precise engineering and deep industry understanding. This innovative design represents significant advancement in industry-wide concerns like particulate contamination and container integrity over traditional cryobags. To celebrate this one-year milestone, we interviewed Adam Shields, Senior Product Development Scientist, at BioLife Solutions and the lead designer behind the CellSeal CryoCase.
Meet the Designer: Adam Shields' Journey from Research to Real-World Solutions
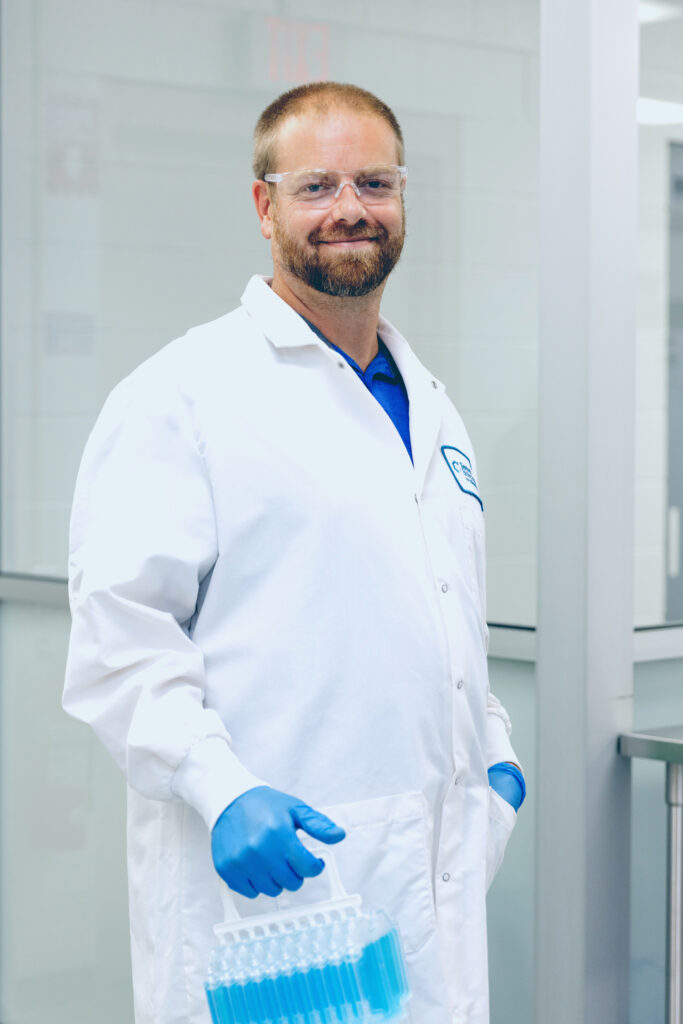
Adam began his scientific career with a PhD in Physics from the University of North Carolina at Chapel Hill and completed an NRC Postdoctoral Fellow at the U.S. Naval Research Laboratory. He then served as a Research Scientist at Cook Medical and subsequently at Cook Regentec, focusing on early device concept development in hemodialysis, orthopedics, and regenerative medicine. Adam’s professional journey demonstrates his commitment to bridge the gap between early phase concept development and tangible, market-ready products.
In this interview, Adam shares insights into the rigorous product development life cycle, material selection considerations, and his vision for future BioLife product developments.
Inside the Innovation: An Interview with Adam Shields
Q: Can you tell us how you transitioned from scientific research to product development?
Adam Shields: It was an organic and gradual process. I started strictly in applied research, developing new tools and writing papers. Each subsequent role has brought me a step closer to the commercial aspects of product development. When Sexton Biotechnologies was founded (later acquired by BioLife Solutions), it presented an opportunity to take ownership of products through the full development cycle, from concept to commercialization.
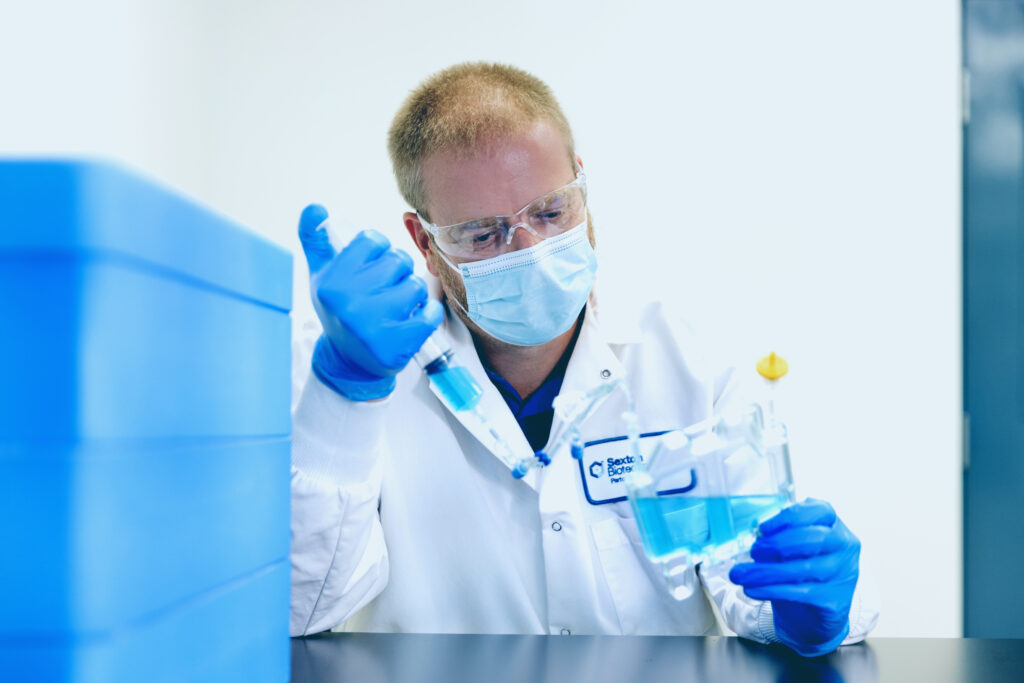
Q: What sparked the development of the CellSeal CryoCase?
Adam Shields: For some time, we had recognized a clear customer demand for cryostorage containers with a larger capacity than our existing CellSeal Cryogenic Vials. When BioLife Solutions acquired Sexton, this created an impetus in terms of resources and timing to move the project forward. The goal of the CryoCase is to improve on cryobags, which are a legacy storage solution badly in need of disruption. The customer need for cryostorage solutions that are more robust, more efficient in manufacturing, and easier to implement in automated processes informed the design.
Q: What were the key factors in selecting materials for the CryoCase?
Adam Shields: Material choice was somewhat simplified by leveraging our successful CellSeal vial materials, particularly Cyclic Olefin Copolymer (COC). It’s proven effective in protecting samples and reducing particulate contamination with a well-known leachables and extractables profile, all of which is critical for CGT products.
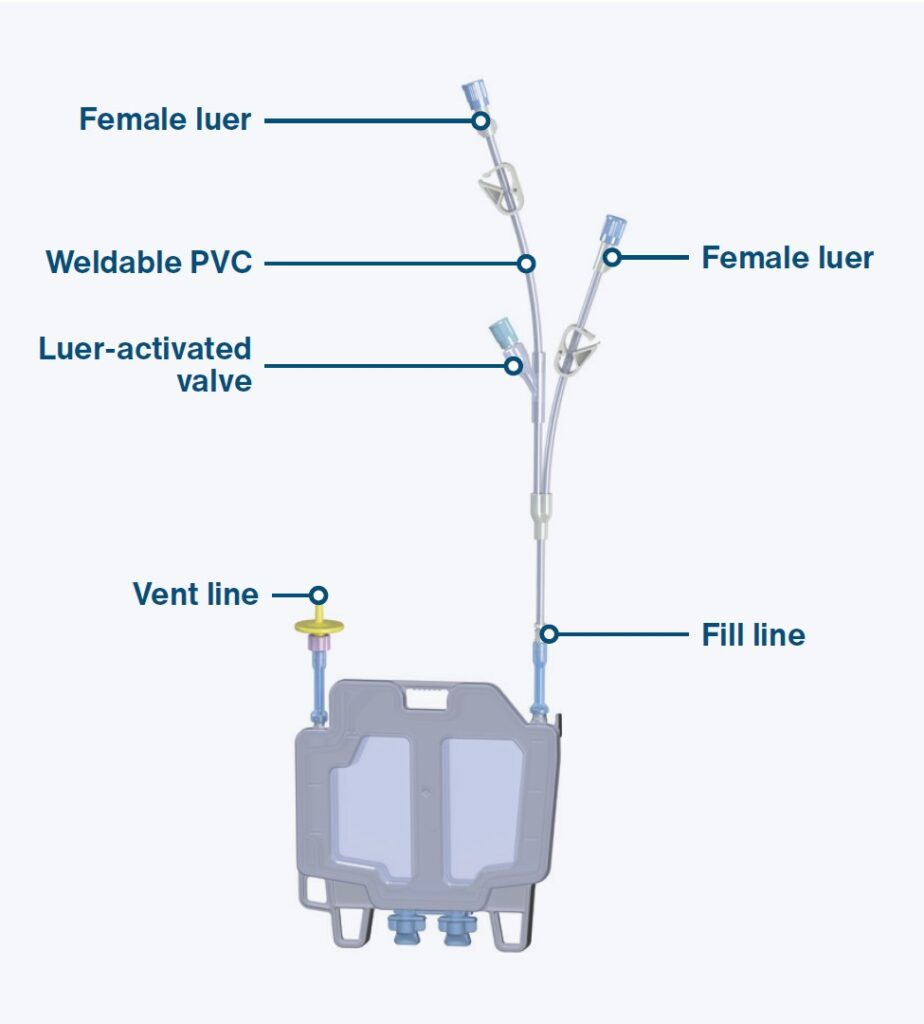
Q: How did you approach designing the CryoCase to ensure it met customer needs?
Adam Shields: In the concept development stage, iteration is key. There were probably hundreds of conceptual iterations, although many of these iterations may just happen in my mind or through simple sketches. Early on we explored a variety of form factors, but determined (relatively quickly) that a cassette form factor was the best approach for several reasons: 1.) It fits many existing storage setups, and 2.) It can scale to larger volumes effectively while maintaining a consistent freeze/thaw profile. Vials do not, and this is critical for sample viability.
Q: How important was real-world testing and validation in the CryoCase development?
Adam Shields: “Real-world” is kind of a stand in for “worst-case scenario”, making this type of testing essential. Early on, many prototypes were tested by throwing frozen containers onto cement floors (sometimes in my own garage) to evaluate their durability. Later, more sophisticated testing confirmed that our rigid design significantly reduced fracture and leakage risks commonly observed with traditional cryobags.
Q: Can you describe any significant design challenges you faced and how you overcame them?
Adam Shields: A major challenge involved designing the retrieval spike ports. Spike ports are designed for the soft plastic to flex and expand as a spike enters the port, creating a press-fit seal. Very close to the design freeze stage in product development, we realized we may have had too much rigid material surrounding the soft spike port material, preventing the stretch. This could potentially impact the seal around the spike. We had to go back to the drawing board, rethink the design, and implement an alternative material, while trying our best to avoid delaying the project timeline.
Q: What differentiates the CellSeal CryoCase from other storage solutions?
Adam Shields: Its primary differentiator is the rigid, fracture-resistant structure, which dramatically reduces the possibility of fractures and leaks from handling when compared to cryobags. It’s designed specifically for the high-value CGT products manufactured by our customers, where issues like sample integrity and particulate contamination can directly impact patient outcomes. The transparency of the container also significantly enhances inspectability, which is crucial for maintaining quality control.
A Year of Success: Real-World Performance and Customer Feedback
One year post launch, studies confirm the CellSeal CryoCase’s superior performance. Evaluations by companies like Immatics Biotechnology and Charles River Laboratory have demonstrated the CryoCase’s fracture resistance, ease of handling, and equivalence in preserving cell viability and recovery compared to traditional cryobags and vials.
Fracture Resistance: In drop tests, the CryoCase maintained integrity even after multiple impacts, significantly outperforming traditional cryobags.
Cell Recovery: Independent studies have shown consistent cell viability, density, and recovery rates, validating the CryoCase’s practical benefits.
Moreover, customers have reported significant operational improvements. The CryoCase design simplifies the filling process, reduces handling complexity, and enhances product inspection, addressing major industry pain points related to container handling and particulate detection.
Looking Ahead: The Future of Biopreservation at BioLife Solutions
Adam and the BioLife team remain committed to continuous innovation. Adam noted there are ongoing material evaluations and system accessory designs to further optimize CellSeal CryoCase performance. His experience with this project underscores the importance of meticulous design and rigorous testing that is grounded in deep industry experience. Stay tuned as Adam and BioLife Solutions continue to lead the way in biopreservation innovation, shaping a safer, more efficient future for CGT storage.